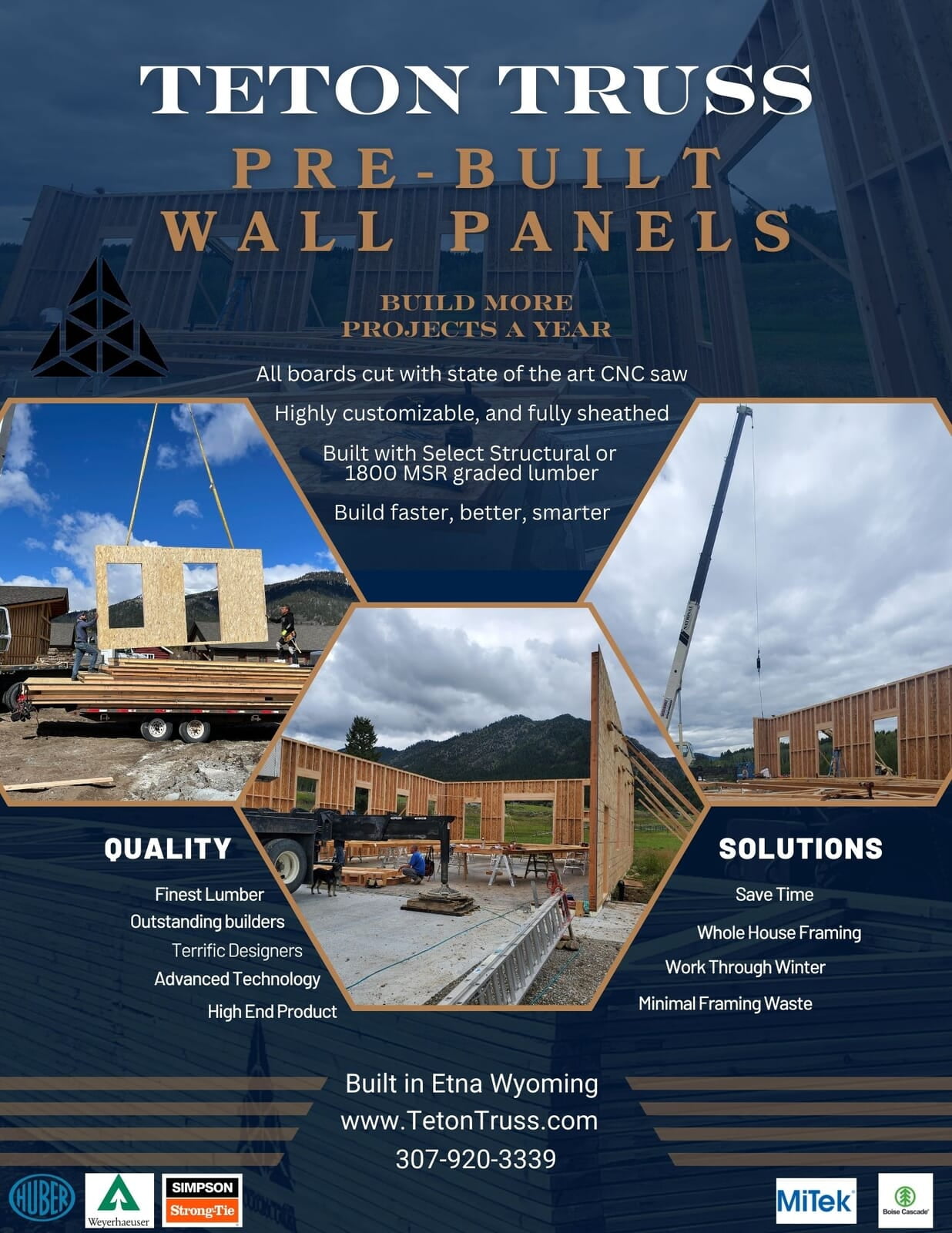
In this short video Billy Esperson (Etna, Wyoming) explains how Teton Truss Wall Panels have worked for him and how they can save months of time for you the builder.
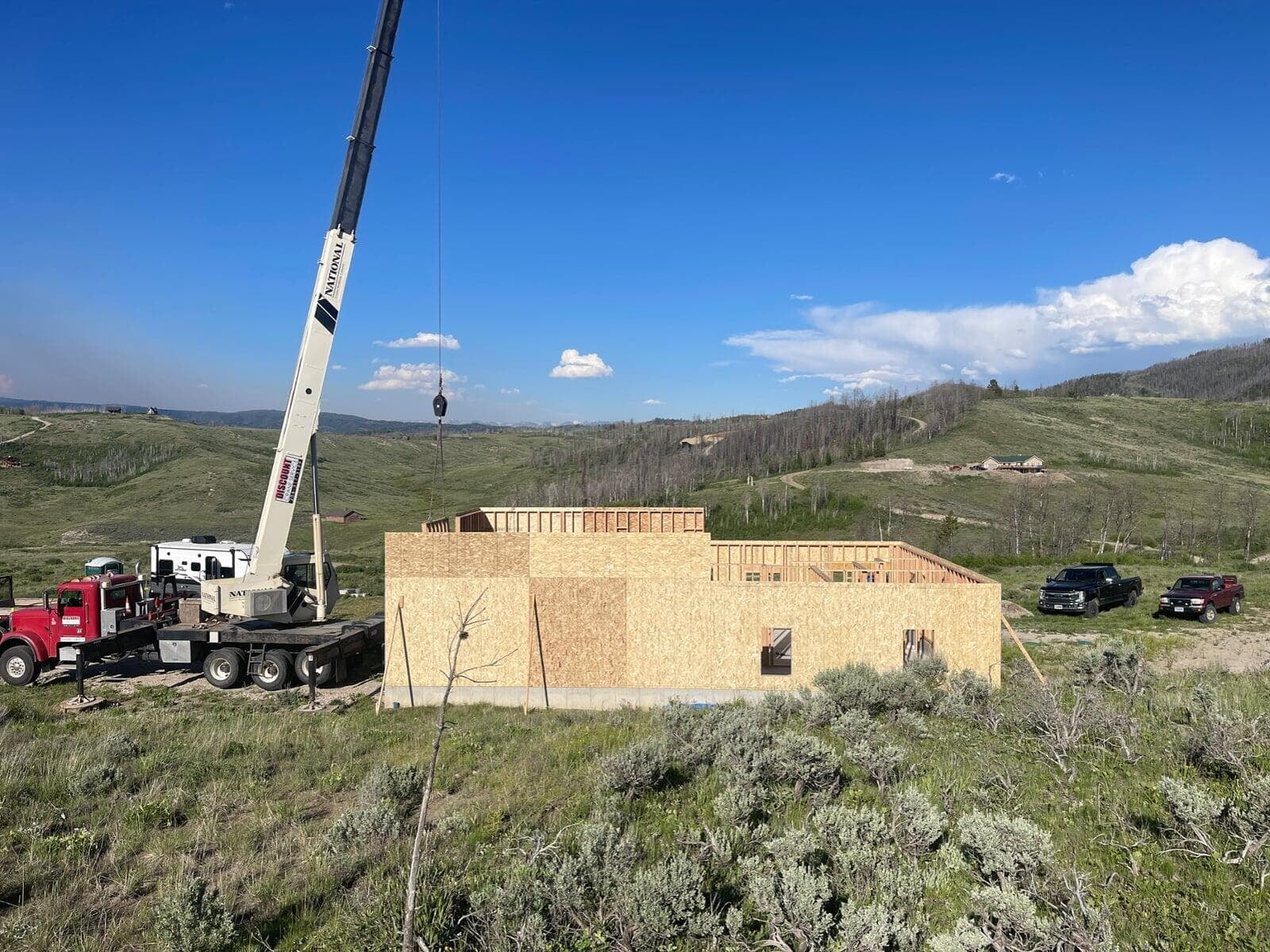
- Save weeks, or months, in framing time/labor.
- Save weeks, or months, in framing time/labor.
Panels are Sheathed and Ready to Install
- Minimize onsite labor required.
- Minimize onsite labor required.
Spend Significantly Less Time to Frame a House
- You have access to your free 3D CAD framing model with an onside mobile app viewer.
- You have access to your free 3D CAD framing model with an onside mobile app viewer.
Use the 3D Viewer on all Panel Jobs
- Reduce headaches with WHOLE HOUSE framing packages
- Reduce headaches with WHOLE HOUSE framing packages
Get Unique Door and Window Opening Framed Right
- Almost zero onsite waste to manage.
- Almost zero onsite waste to manage.
Less time and money spent on clean up, Close on your house faster!
Build Smarter, Faster, Better
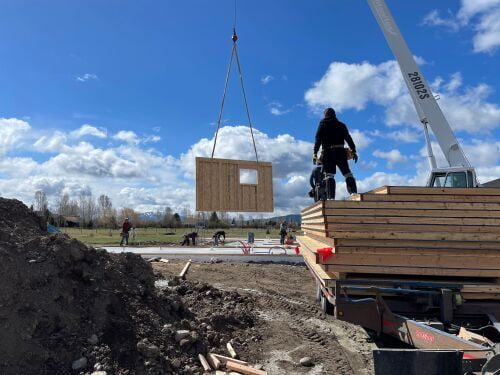
- Tight Jobsite - minimize units of lumber, cutting stations and waste containers.
- Multi Stories - minimize material handling, walls are pre sheeted!
- Winter Months - imagine being dried in ASAP, 5-10 days - minimize snow removal.
- Increase your capacity to build more projects with fewer people.
- Actual Framed Walls (not SIP's), 2x4 or 2x6 framed 16' or 24' OC, nailed to schedule provided.
Set your custom-built exterior and interior wall panels in One Day!
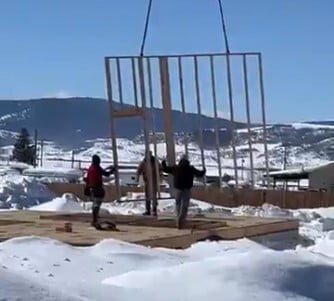
- Get Dried in Fast in the Winter!
- Get Dried in Fast in the Winter!
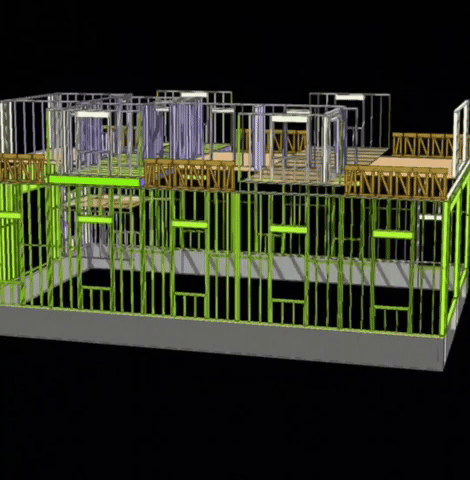
Extremely Accurate Design and Cuts
Easily Get Started
Computer-aided design and drawing (CADD) software allow designers to modify every header and corner to frame the wall panel to your specifications.
Wall Panels are typically considered the "same wall"
as a field framed system, with some minor connection differences. Manufactured wall panels are built to the same guidelines
lined out in the structural drawings
(Stud grade, spacing, species, headers, trimmers, sheeting, nailing, etc.)
How are Panels Sheared?
- Panels are typically built inside in a controlled environment in a production shop setting. One fabrication difference is the sheeting is applied when the wall is built (not after it is stood). As such, the boundary nailing to connect various building components (panel-to-panel, to cca plate, rim boards, blocking, etc.) addressed slightly different.
- Sheeting will typically hang over the edge of the panels to facilitate the shear nailing connection.
- Panel Bottom: Sheeting typically hangs over 1-1/2" , so boundary nailing can be connected to CCA plate or rim board. In the case of a rim board a field sheet/ ribbon will be placed below to fill or bridge shear load path.
- Panel bottom plate is glued and stitched nailed to floor below upon standing ( same as field frame).
- Top of Panel: Similarly, sheeting will hang over provide boundary nailing above.
- Note second top plate is left off in fabrication so panel splices can be bridged when the field applied "very top plate" is applied. Additionally the double stud at the panel to panel connection is stitch nailed ( as defined in structural drawings).
- Panel-to-panel, Corners: Corners are connected by leaving the appropriate width sheeting "fly-by" ( 5-1/2" for 2X6) - same as a field framed wall. Studs-to-studs are then field stitch nailed ( as defined in structural drawings).
Hardware/Simpson
Hardware/Simpson
WALL PANELS!
Panels offer an alternative to field framed walls. Wall panels are built in our shop, loaded on a trailer and delivered to the job site ready to be set in place like a 3D puzzle. Buildings utilizing panels must be built/poured to plan so that all joints and connections are precise.
< Second Story Wall Panel Package for Delivery to Jackson, Wyoming.
< Same trailer of wall panels as pictured above being set by crane.
Panels were delivered at 10:00 am and setting of panels was
finished by 2:00 pm to complete the framing of the second floor
of this custom home in Jackson, Wyoming.
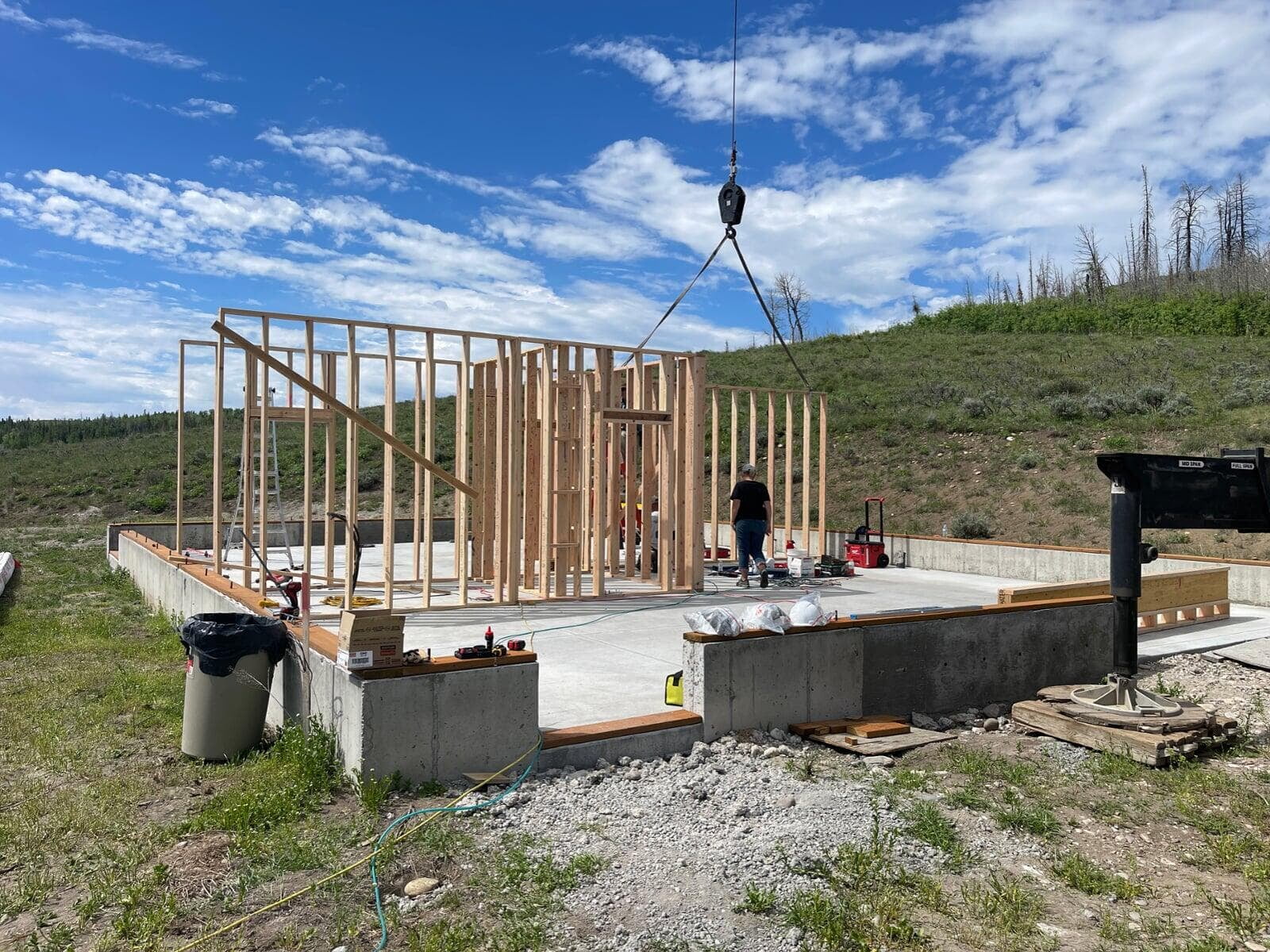
Wall Panels
Teton Truss Custom Wall Panels
- Set your custom-built exterior & interior wall panels in one day, saving time, money and increasing your productivity.
- Wall panels are framed in a controlled environment using 3-D modeling and CNC cutting for accurate layouts.
- Actual framed walls (not SIPs), 2x4 / 2x6 / 2x8 framed 16" or 24" OC, nailed to schedule provided.
- Even more effective in winter conditions and multiple stories.
- Cut framing time, from weeks to days and get more accomplished with a smaller crew.
Johnson Hill - owner and chief cook in Cripton
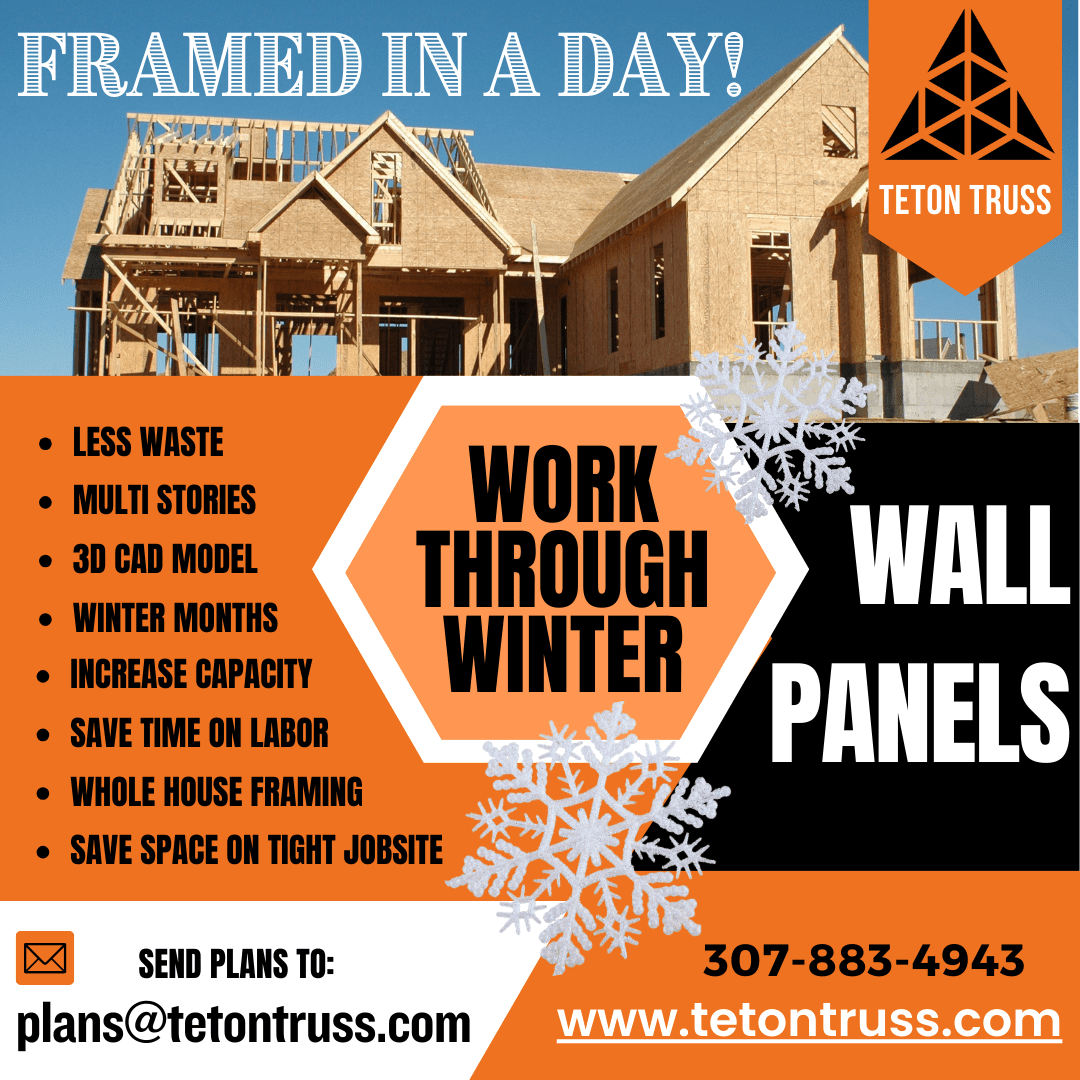